Elite Robots automating salt core production
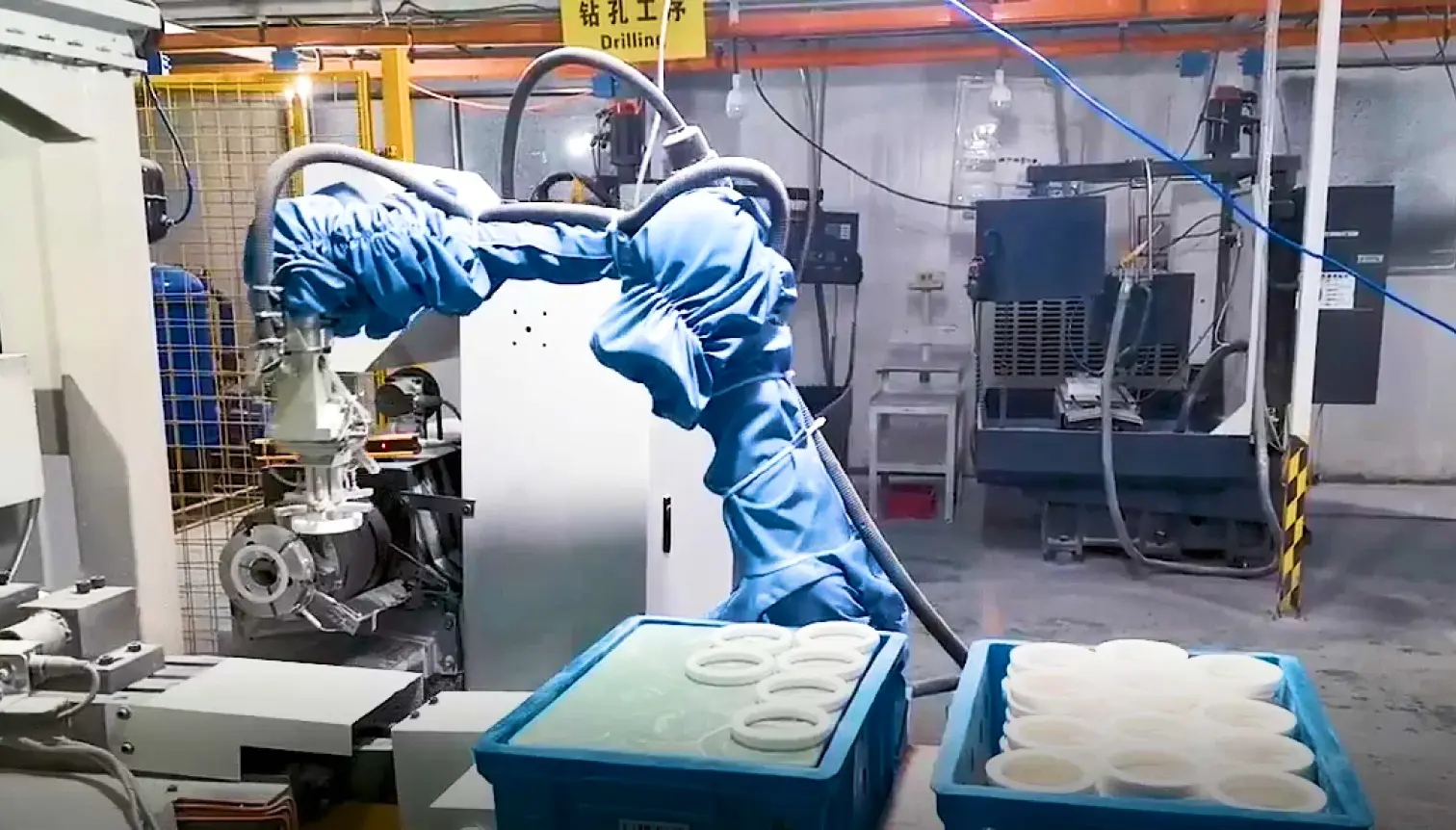
Client
The customer is a North China mechanical manufacturing company for the automotive industry. The enterprise mainly produces wear-resisting inlaid ring, salt core and stainless-steel parts which then supplies to global manufacturers such as Mercedes, BMW, Volvo, Toyota, Honda and other well-known international automotive enterprises.
The parts are used both to supply the Chinese production facilities of the above companies and exported abroad, including the United States, Japan, Germany, India and Brazil.
Requirements
The workshop environment for the salt cores’ manual refining was not optimal for workers due not only to the frequent noise caused by the presence of the numerous production equipment, but also the large amount of dust inside the working environment caused by the salt cores refining process, which in the medium to long term could lead to negative consequences for workers’ health.
In addition, the manual work required concentration and precision, and threatened to become increasingly inaccurate after a few hours due to worker fatigue.
With all this in mind, the manual production process seemed ideally suited to automation, in order to improve quality and optimize processes, as well as protect the health of workers by keeping them away from suboptimal areas.
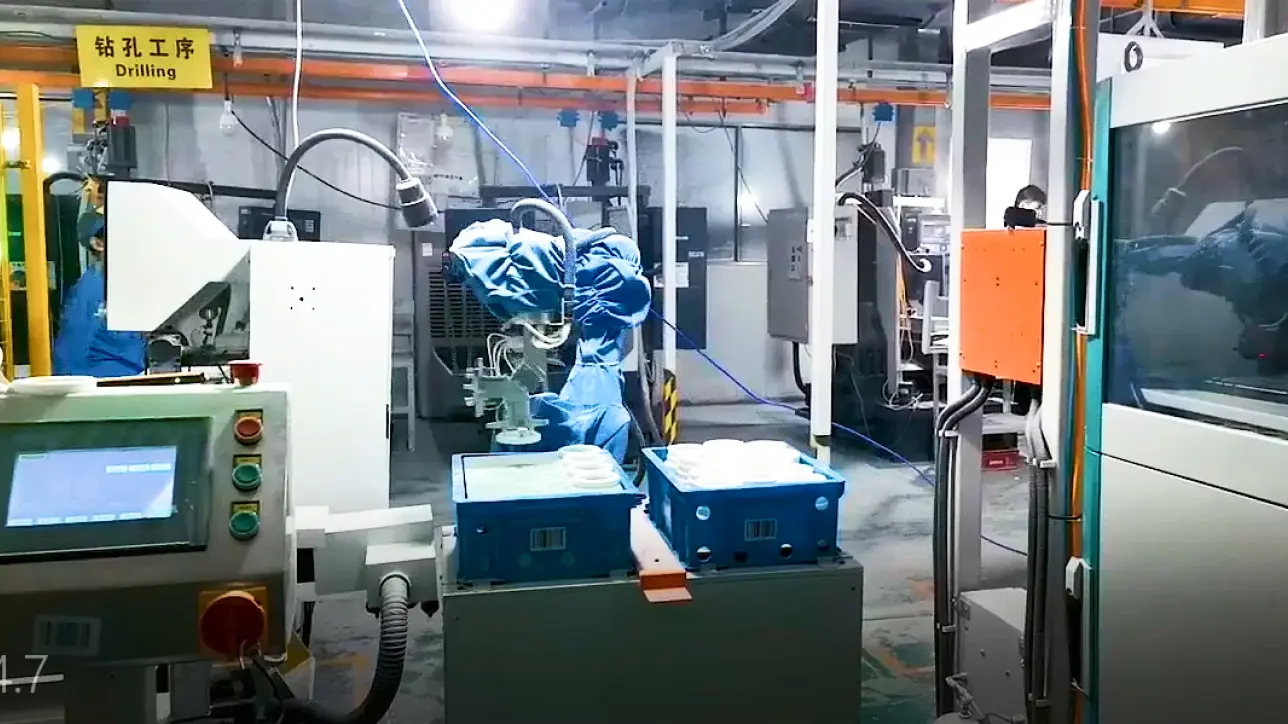
Solution & Benefits
The company, therefore, opted for a fully automated system with robot arm and, after a continuous evaluation, communication, and field investigation, Elite Robots eventually recommended to the company to adopt the EC66 collaborative robot model integrated with a 3D camera.
The cobot was equipped with a gripper with two interchangeable gripper jaws (or end-of-arm tools). In this way, the cobot can correctly pick up both the raw salt cores as well as the refined ones (which after the process are smaller in size) by simply swapping the jaws.
The 3D vision system was installed on top of the pile of raw salt cores and integrated with Elite Robots robotic arm. Thanks to such an integration of camera and cobot arm, the cobot can perfectly locate and grasp the raw salt cores to be processed, despite the latter being stacked irregularly.
The repeated positioning repeatability of ±0.03 mm of Elite Robots’ cobot enables an orderly placing of the salt cores both in the CNC machine prior to the refining process and in the finished product pile after the process.
Despite the harsh working environment, the IP54 level of protection (the cobot will be protected against contamination from limited amounts of dust and other particles) of the robotic arm was able to meet expectations. However, it was decided also to equip the robot with a special protective suite in order to further reduce the impact of dust generated by the refining process and ensure the long-term stability of the workstation.
Due to the cost-effectiveness of the entire solution, the zero-maintenance required and the very low operating costs (with power consumption of 250 watts on average, the cobot consumes less electricity than a heat lamp!) the customer achieved a full payback on its investment in only 7 months after installation.