Empowering the metal industry with cobots
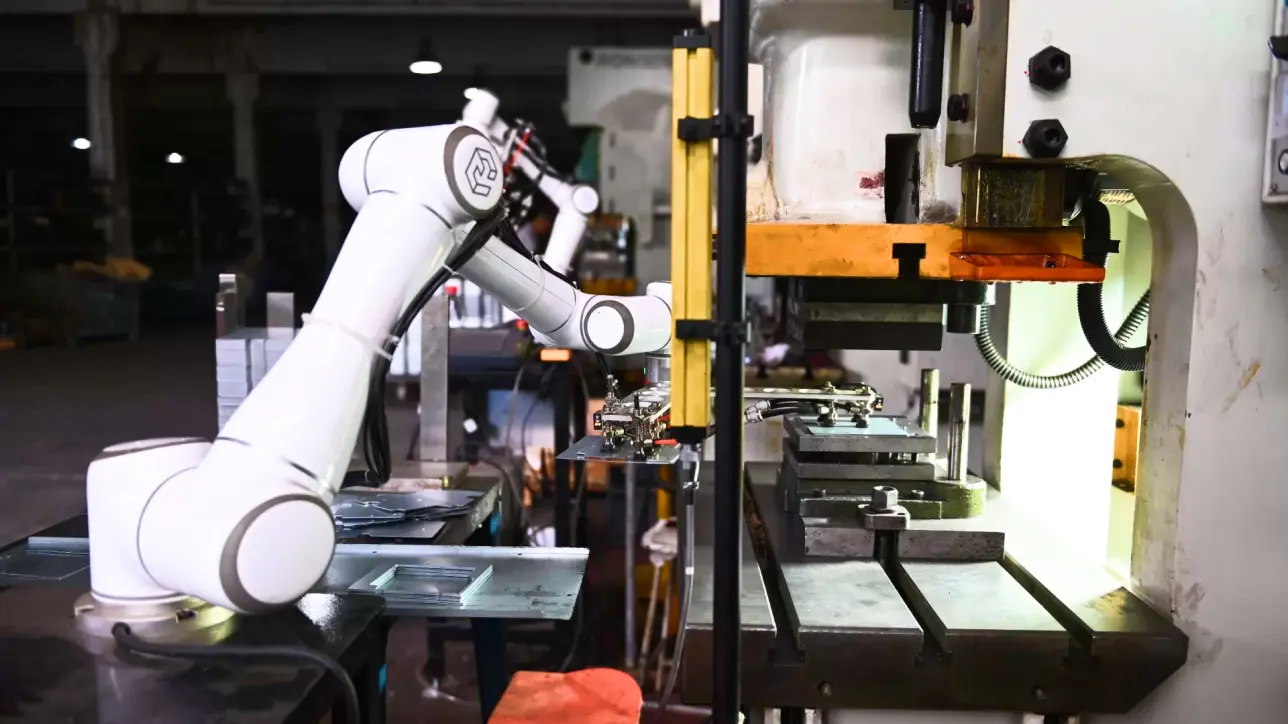
Background
Gaotong Machinery is an established SME from the city of Qingdao, in Northern China. The factory focuses on the production and processing of household air-conditioning sheet metal parts, high-speed rail accessories, and medical equipment sheet metal parts, and has accumulated a lot of experience and technologies in the air-conditioning sheet metal industry. The client has been widely recognized by consumers for its stable processing repeatability and quality.
In recent years, the factory has been keeping pace closely with industrial trends and constantly pursuing industrial automation. In 2002, the factory imported its first AMADA CNC punch from Japan, and since then, it has been increasing investment in automation equipment. As robot technology becomes mature, the factory introduced six-joint industrial robots for welding devices and adopted the automation solution with six-joint handling robots in 2014.
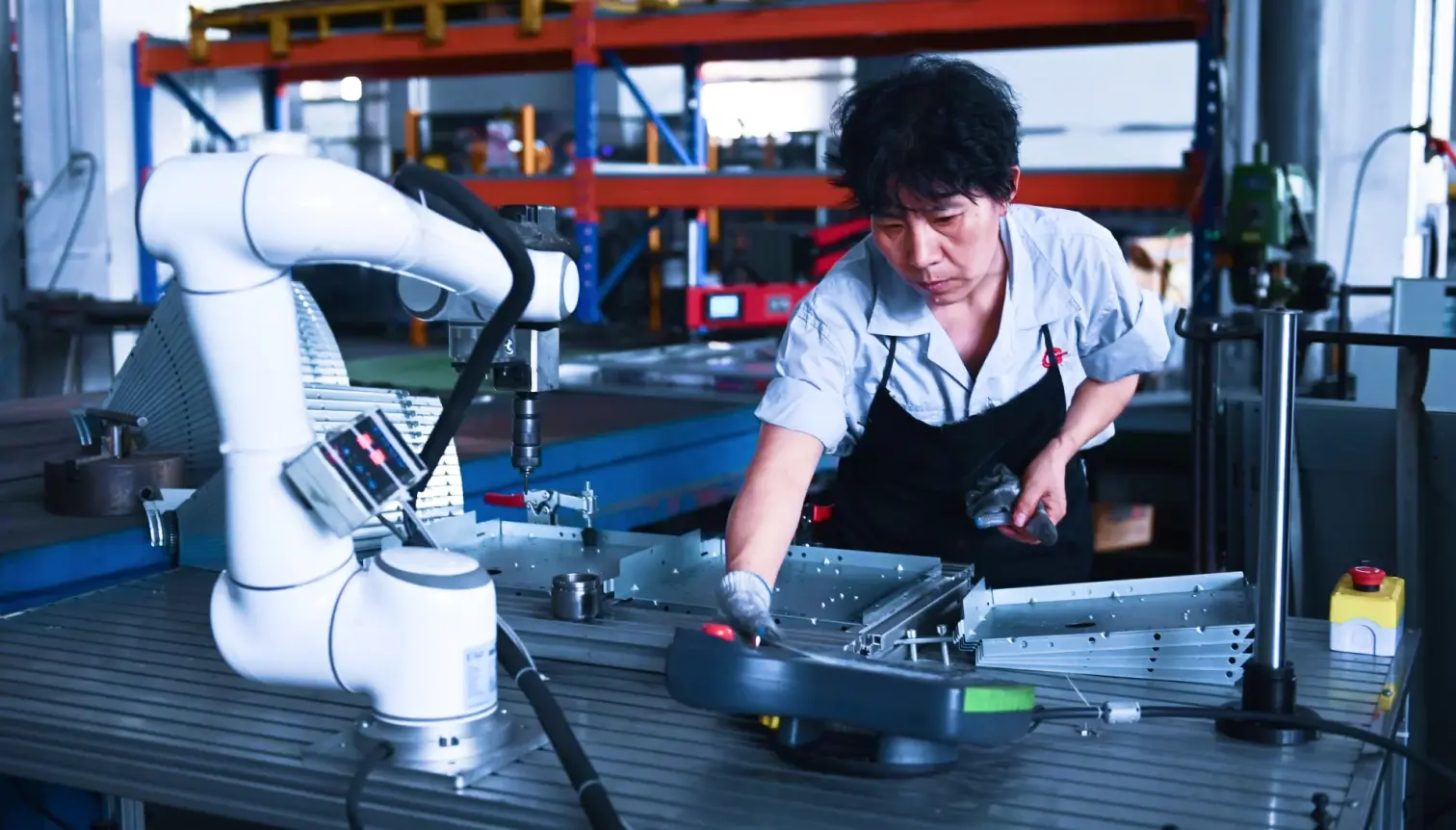
Pain Points
Due to the increasing customization needs at the consumer end, the production line of Gaotong Machinery faced the challenge of small-batch and multi-variety, which led them to reconfigure and reprogram the robots for new tasks very often. However, the traditional six-axis industrial robots originally deployed by the company in their production line strongly slowed down the production process due to their long switching cycle.
Solution & Benefits
On the other hand, redeploying a cobot and switch it between multiple machines takes much shorter time (no more than half day). Also, collaborative robots are more user-friendly than industrial robots, not much slower and when processing some specific workpieces can be even faster! Therefore, in 2016, the company gradually replaced most of its traditional industrial robots with collaborative robots, eventually deploying up to four Elite Robots collaborative robots for its pick & place, palletizing, and tapping tasks.
In the tapping application, there are some components where up to 120 holes need to be threaded, and because of the monotony and repetitiveness of this work, manual operators often miss some holes, leading to a high product failure rate.
Using Elite Robots collaborative robots, on the other hand, not only reduces the timing of the tapping process, but also, and most importantly, ensures that no hole will be missed.
Since Gaotong Machinery has been using Elite Robots cobots, the efficiency of their production line is greatly improved, and their future direction is to use them for more tasks which are now still performed by either humans or industrial robots. In an era when time is money, Elite Robots cost-effective, efficient and easy-to-configure collaborative solutions have been winning the approval of this and many other clients on the road to automation upgrades!